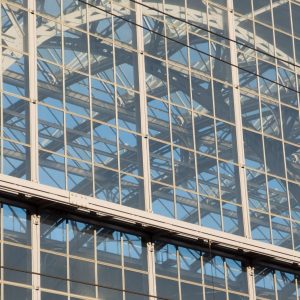
Lasers can be used to bond metal and glass
An exciting new technology has been developed by scientists at Heriot-Watt University in Edinburgh that enables glass and metal to be welded together using lasers.
The difficulty with attaching glass to metal previously rested in their differing thermal properties. Glass was liable to shatter when using conventional bonding methods involving heat; therefore, metal bonding adhesives have been employed. These glues can degrade and become unreliable over time, meaning that durability is limited. This is why companies that install Bifold doors swindon way will ensure that the glass in situ on the doors is firmly in place. The use of lasers in this types of welding is an exciting development for all those who work in similar industries offering bifold doors and other glass products.
Ultrafast laser
The new technique uses an ultrafast laser system that creates an area of extreme heat. This melts both materials and allows them to fuse together. The laser provides pulses of one million watts for just one trillionth of a second each time.
The director of the Heriot-Watt EPSRC Centre for Innovative Manufacturing in Laser-Based Production Processes, Professor Duncan Hand, believes the ability to weld metal to glass is a huge advancement and will enable more flexible design. The centre, which is also known as CIM-Laser, is working on the project with teams from both the public and private sector with funding from Heriot-Watt, Innovate UK, and other industrial partners.
Image Credit
Whilst there may be advances in a number of industries with this technology, metal adhesives still have a vital role to play, particularly in relation to bonding metals to other materials. Strong, effective adhesives can prevent the need to drill or bolt materials together.
Diverse potential
The new ultrafast laser system can also be used to hermetically seal flexible glass and is expected to be used for entirely original products in such diverse industries as defence, healthcare and aerospace. Experimentation with the laser has led to not only glass but also quartz and sapphire being welded to stainless steel, aluminium and titanium. Images of some of the welded pieces are aesthetically very pleasing, potentially meaning that an artist may utilise this technique in time.
The work the team has completed so far has been robustly tested, with welded items remaining complete at between -50°C and 90°C. This indicates that the laser produces a bond capable of surviving in extreme conditions. The value of this new process is potentially very high, particularly because of the new innovations that may be possible with this technology. There is certainly some exciting work to look forward to.
Leave a reply